Materialise Magic’s Ansys simulation
Increase the quality of your printed parts and minimize production errors by optimizing the metal additive manufacturing (AM) process with the Magics Ansys simulation module.
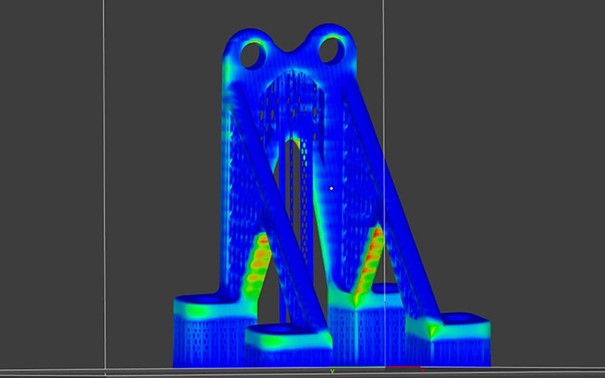
- Shorten time-to-market
- Minimize waste
- Improve product quality
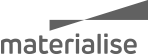

4 reasons in favor of the Ansys Simulation Module
- The module is easy to use and you get accurate results even without expert knowledge
- Evaluate AM-relevant results and improve your data preparation through seamless integration into the Magics workflow.
- Use of market-proven high-end AM simulation technology based on the Ansys solver
- Increase AM-ROI with an affordable software module for 3D metal printing
Main features
Analyze the deformation of components to optimize the position and adjustment of support structures. Minimize expensive test prints, accelerate time to market and reduce development costs.
Identify the risks of building large parts that are susceptible to residual stresses and deformations. Identify design errors using reliable AM process simulations.
Avoid overheating and achieve better surface quality. Generate compensated component geometry to improve geometric accuracy.
Optimize part orientation for AM processes and add only necessary support structures. Use the simulation results to make well-founded decisions for part preparation.
Frequently asked questions (FAQs)
Which materials can be simulated?
All common 3D printing materials such as aluminum, titanium or various steels can be simulated.
Do I need knowledge of materials science to use the software?
The module is integrated in Magics and deliberately kept very simple so that even a layman can obtain and interpret accurate results.
Where does a simulation make the most sense?
Simulation makes sense for all components. The advantages are most noticeable with very large, time-consuming components, components with thin walls and components made of expensive materials such as titanium.